μ-MIM® Technical Newsletter Vol. 23: The analysis for alloy developments
Alloy development using EBSD
Electron Backscattered diffraction (EBSD), is an epoch-making crystal analytical method and widespread in the late 1990s to 2000s, thanks to the great improvement of calculation speed in the operation computer, attached to the EBSD system. The EBSD analysis device is installed with scanning microscopy (SEM), which is the same as energy dispersive spectrometer (EDS) analysis device. The important feature of EBSD is crystal orientation determination in every single crystal grain. The orientation will be shown using the colour map, therefore, it is possible to observe the phase distribution or aggregate structure and eventually to calculate the proportion of phases. According to the computer system and software development, the blank area near the grain boundary is minimised and high-resolution analysis available.
Our titanium alloy observation example
We deploy EBSD for a new titanium alloy development, in cooperation with an external institute. The mechanical property of titanium alloy is determined by the construction ratio between α-phase and β-phase. Therefore, EBSD is indispensable to confirm the composition and crystal phase distribution, which support the mechanical property test result theoretically. The images below are an example of titanium alloy specimen EBSD analysis data. The crystal size and phase are clearly observed. The basics of EBSD is observing “Kikuchi pattern”, which is already known a long time in crystallography history, however, it consumes a huge amount of time to determine the phase if there is no computer-aided system. Currently, EBSD is widely and commonly applied for material development, which seemed to be unimaginable decades ago. It might be also feasible to develop super-alloys with the help of this technical evolution.
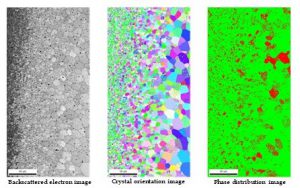
Column
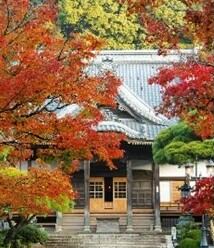
The season with autumn leaves is one of the most favourite periods in Japan. There are visitors on the popular mountains to enjoy hiking under the vividly coloured leaves. The whole atmosphere in nature makes our appetite increase so, in Japanese, there is a phrase “Autumn appetite“. Coloured leaves are found not only on mountains but also in parks, streets, temples and shrines, overall. In recent years, foreign tourists pay more attention to the harmonized beauty in Japan and it becomes the second “hottest season” for travelling. It would be worthy to consider visiting Japan in this season after the corona pandemic calms down.
Conclusion
Cracking, slumping or blistering is commonly observed due to the binder swelling and/or residual stress difference between the surface and interior. It is possible to avoid these problems by selecting appropriate organic solvents and temperature control.
The catalytic deboning uses sublimation of binder, thus it is possible to decompose the binder in relatively short processing time with minimizing the deformation. However, with a strong acidic atmosphere, theapplicable metal material option is limited.
In the sintering process, the necking, which is bridging the metal powders by thermal diffusion, starts at the sintering temperature. Once the necking starts, the shrinking is observed and increases the density, thus before starting the necking reaction, all the organic components should be decomposed and gas between the powders should be removed. In the sintering process, the unwanted chemical reaction, such as oxidation or carbonization, leads to mechanical property loss, therefore a precise atmosphere control with low heating rate at the beginning of the process is required. Also, when it reaches the sintering temperature, some add it vegetal can be evaporated.