μ-MIM® Technical Newsletter Vol. 27: Tungsten (W) application in MIM
Recently we received W related inquiries more than before. In this issue, we will introduce our W application in our μ-MIM® technology.
About W
It is well known that W has the highest melting point among practical metal. The melting point is around 3,400 degC and the specific gravity is 19.25, which is similar to gold (Au, 19.35), which is 2.5 times larger than iron specific gravity. Additionally, W is easy to plate Au, thus in the past, W was used for producing counterfeit bars, unfortunately. W is mainly applied to tooling instrument, due to its high hardness at elevated temperature. Also, W was familiar with the light bulb filament before LED light bulb domination in the market. Now, the W filament is no longer applied to light bulb but to discharging electrodes in air-purification equipment or printer. Another characteristic property is a high radiation shield ability. This property is well applied in the medical field, for example, the W sheet is applied to the X-ray CT radiation shield and the W marker is used in the catheter-based operation. W is reserved all over the world but the high purity law material for commercial use is produced in China and the market share is more than 80%. Therefore W becomes strategic material same as the rare earth element, from time to time.
(Reference: http://www.jtmia.com/index.htm,https://www.nittan.co.jp/)
Processing and sintering of W product
W has a high melting point, this it is impossible to take some dissolution method as other metal material. First, ammonium paratungstate (APT) is produced from the W ore and the APT will be torrefied to tungsten trioxide (WO3) and hydrogen redacted to be pure W powder. Finally, the W powder will be compacted and sintered by the powder metallurgy method to compose the W ingot. The W ingot will be transformed into sheets, wire, powder and other shapes by applying mechanical force. The W alloy is also produced by the powder metallurgy method. The additional element powder is mixed and elevated the temperature above the melting point of the additional element. The liquid of the additional element surrounds the W powders and sintered. The microstructure of the W alloy looks sea-island structure.
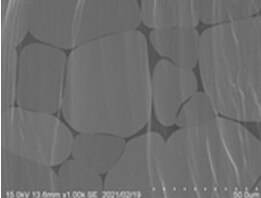
MIM development
According to these characteristics of W, metal injection moulding (MIM) can be the best solution for W parts production. However, it is required binder development and sintering programme optimisation for the W MIM production and a very limited number of interests were showed for complicated small W parts in the past. Because of these facts, the W MIM components were not distributed in the market until a few years ago, but now, especially in the medical industry, W MIM inquiry is increasing for the small complicated designed W parts serial production. We have experienced some W alloy MIM component production but at the same time, we are developing our technology to increase the W alloy material options.
Column
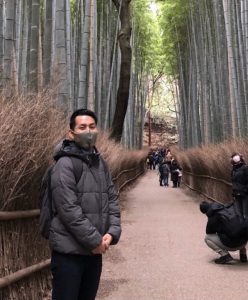
I am Nakata from the Production department and I am responsible for the sintering section. I am learning how to improve production efficiency through the furnace maintenance work and quality control of sintered parts. When my Kaizen suggestion is approved and deployed to the actual production line, I felt happy for bearing fruit in my works. I like exercises and on weekend I normally play football and go cycling with my friends. However, due to the situation, I have changed my exercise to hiking. I go to Arashiyama, Kyoto area to see the famous temples and scenery. I wish I will be able to take our customers from abroad to those beautiful places soon in the future.
Conclusion
Cracking, slumping or blistering is commonly observed due to the binder swelling and/or residual stress difference between the surface and interior. It is possible to avoid these problems by selecting appropriate organic solvents and temperature control.
The catalytic deboning uses sublimation of binder, thus it is possible to decompose the binder in relatively short processing time with minimizing the deformation. However, with a strong acidic atmosphere, theapplicable metal material option is limited.
In the sintering process, the necking, which is bridging the metal powders by thermal diffusion, starts at the sintering temperature. Once the necking starts, the shrinking is observed and increases the density, thus before starting the necking reaction, all the organic components should be decomposed and gas between the powders should be removed. In the sintering process, the unwanted chemical reaction, such as oxidation or carbonization, leads to mechanical property loss, therefore a precise atmosphere control with low heating rate at the beginning of the process is required. Also, when it reaches the sintering temperature, some add it vegetal can be evaporated.