Benefits of μ-MIM®
What is μ-MIM®?
With our technology, we are able to produce metal components that would not be possible with conventional MIM manufacturing methods. We can produce very small parts with complex shapes from a wide range of materials in large quantities with high precision and quality.
With over 50 years of experience in the industry and more than 25 years of research and development, we are your trusted partner for medical device components as well as parts in the semiconductor and precision industries.
With over 50 years of experience in the industry and more than 25 years of research and development, we are your trusted partner for medical device components as well as parts in the semiconductor and precision industries.
The 4 best reasons to manufacture high-precision components with μ-MIM®
01
High tolerance
The precision level of μ-MIM® technology is almost identical to machining.
With over 25 years of our original μ-MIM technology development, we have achieved unprecedented tolerance satisfaction in an as-sintered state. In conventional MIM, the tightest tolerance is +/- 30 μm, while μ-MIM® achieves +/- 10 μm.
Compared with the latest machining technology, the tolerances achieved are lower, but still competitive with conventional machining. Plus, μ-MIM® technology is a net-shape production technology that uses minimal post-processing to reduce the risk of tolerance deviations in 3D locations. Productivity and preciseness are μ-MIM® technology's unique strengths, which help realise your ideal metal part production to the market.
With over 25 years of our original μ-MIM technology development, we have achieved unprecedented tolerance satisfaction in an as-sintered state. In conventional MIM, the tightest tolerance is +/- 30 μm, while μ-MIM® achieves +/- 10 μm.
Compared with the latest machining technology, the tolerances achieved are lower, but still competitive with conventional machining. Plus, μ-MIM® technology is a net-shape production technology that uses minimal post-processing to reduce the risk of tolerance deviations in 3D locations. Productivity and preciseness are μ-MIM® technology's unique strengths, which help realise your ideal metal part production to the market.
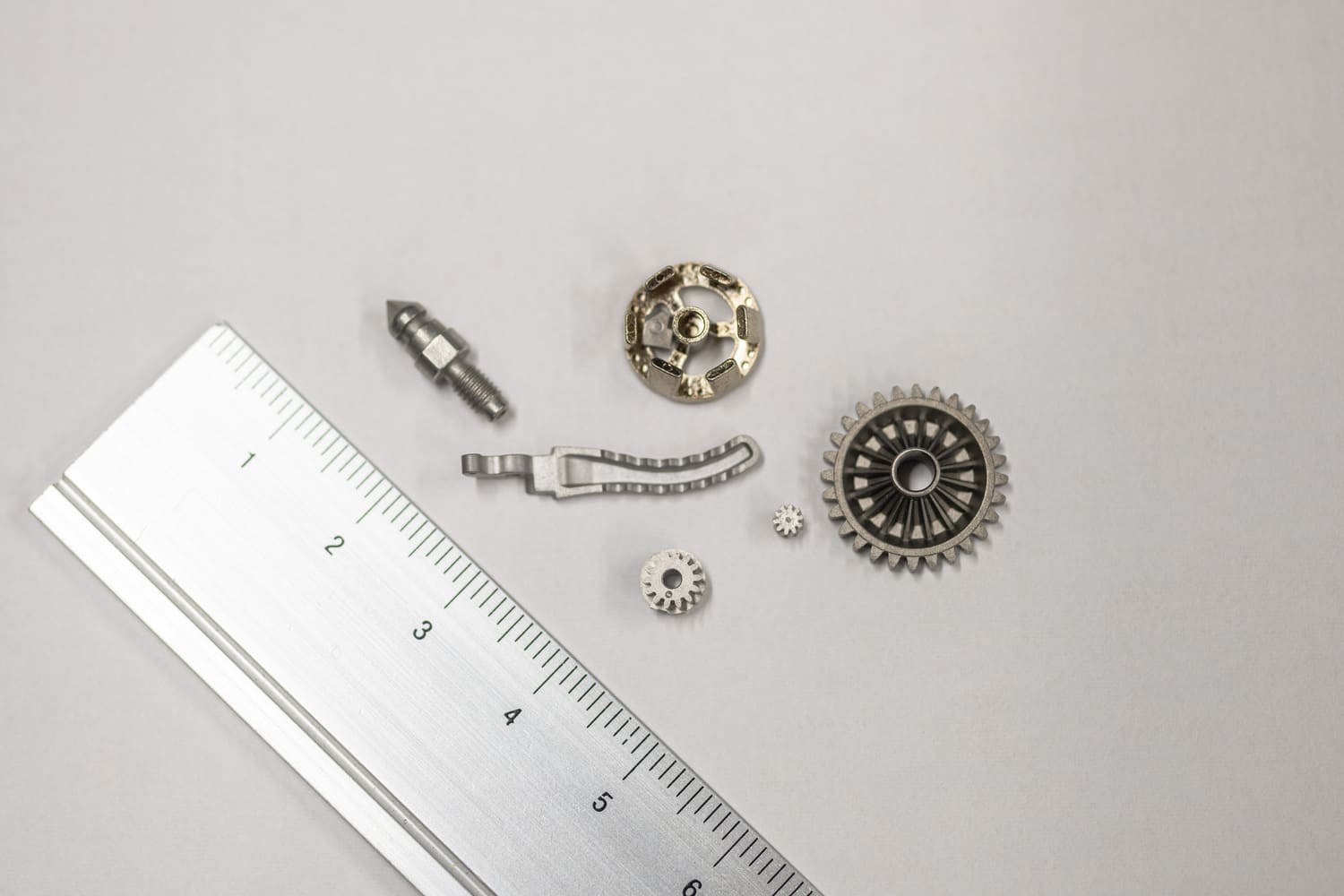
02
Material varieties
μ-MIM® offers you a broad range of materials in the MIM industry.
This is due to our original feedstock processing, which we developed based on our knowledge and experience in plastic injection moulding history.
Since our lead time for feedstock development could be relatively short, newly developed alloy powder can also be used for production, provided the right size and shape of powder is available for procurement.
We are capable to optimise the feedstock for each product's stable production, and newly developed alloy powder can also be used for production.
This is due to our original feedstock processing, which we developed based on our knowledge and experience in plastic injection moulding history.
Since our lead time for feedstock development could be relatively short, newly developed alloy powder can also be used for production, provided the right size and shape of powder is available for procurement.
We are capable to optimise the feedstock for each product's stable production, and newly developed alloy powder can also be used for production.
μ-MIM® experienced material (Trial included)
Stainless steel
304L, 316L, 17-4PH, 410L, 420J2, 440C, HK30, Precipitation hardening by Si
Titanium
Ti, Ti-6Al-4V
Copper
Cu, Nickel silver, Cupronickel
Nickel
Ni, Kovar, Inconel 718
Magnetic
Fe-3%Si, SS410L, PB permalloy, Permandur
Low alloy steel
SCM415
Tungsten
W-Ni, W-ni-Fe, W-Cu
Molybdenum
Mo-Ni
Precious metal
Au, Ag, Pt alloy, Ir, Pd allloy
03
Design freedom
Our 3D-μMIM® technology has been designed to support the high level of design freedom you have come to expect from traditional MIM.
μ-MIM® technology was developed with a focus on serial production of small complex designs, thus with a minimum of additional machining production has been realised.
Because μ-MIM® technology was developed with a focus on serial production of small complex designs, we are able to produce small features or impossible to demold designs with a minimum of additional machining.
Additionally, our 3D-μMIM® technology achieves even a high level of design freedom that you have not expected from traditional MIM.
Our μ-MIM® and 3D-μMIM® technology realise your difficult-to-machined design serial production.
μ-MIM® technology was developed with a focus on serial production of small complex designs, thus with a minimum of additional machining production has been realised.
Because μ-MIM® technology was developed with a focus on serial production of small complex designs, we are able to produce small features or impossible to demold designs with a minimum of additional machining.
Additionally, our 3D-μMIM® technology achieves even a high level of design freedom that you have not expected from traditional MIM.
Our μ-MIM® and 3D-μMIM® technology realise your difficult-to-machined design serial production.
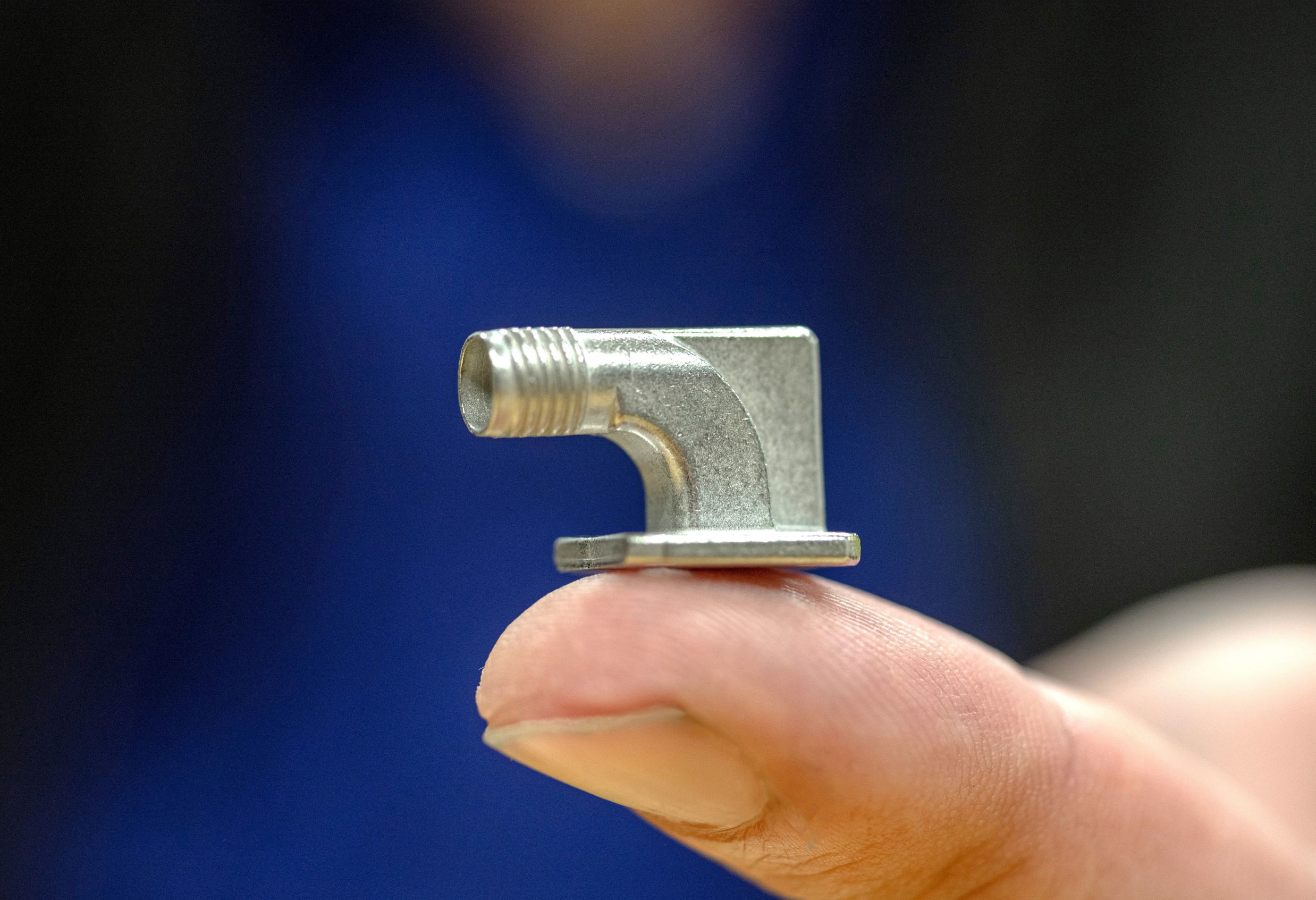
04
Stable mass production
Our careful quality control ensures stable serial production in the requirements of dimensions and mechanical properties.
We know that the production of small, complex metal parts requires even better process control than conventional MIM, because the quality of the preceding step has an even greater influence on the parameters of the following step.
The production of small, complex metal parts requires good uniformity in a feedstock pellet since the product size can be smaller than a pellet size.
We have precisely controlled our production process from feedstock to sintering, plus the final dimensional measurement process under the certified ISO 13485 quality assurance system.
We know that the production of small, complex metal parts requires even better process control than conventional MIM, because the quality of the preceding step has an even greater influence on the parameters of the following step.
The production of small, complex metal parts requires good uniformity in a feedstock pellet since the product size can be smaller than a pellet size.
We have precisely controlled our production process from feedstock to sintering, plus the final dimensional measurement process under the certified ISO 13485 quality assurance system.
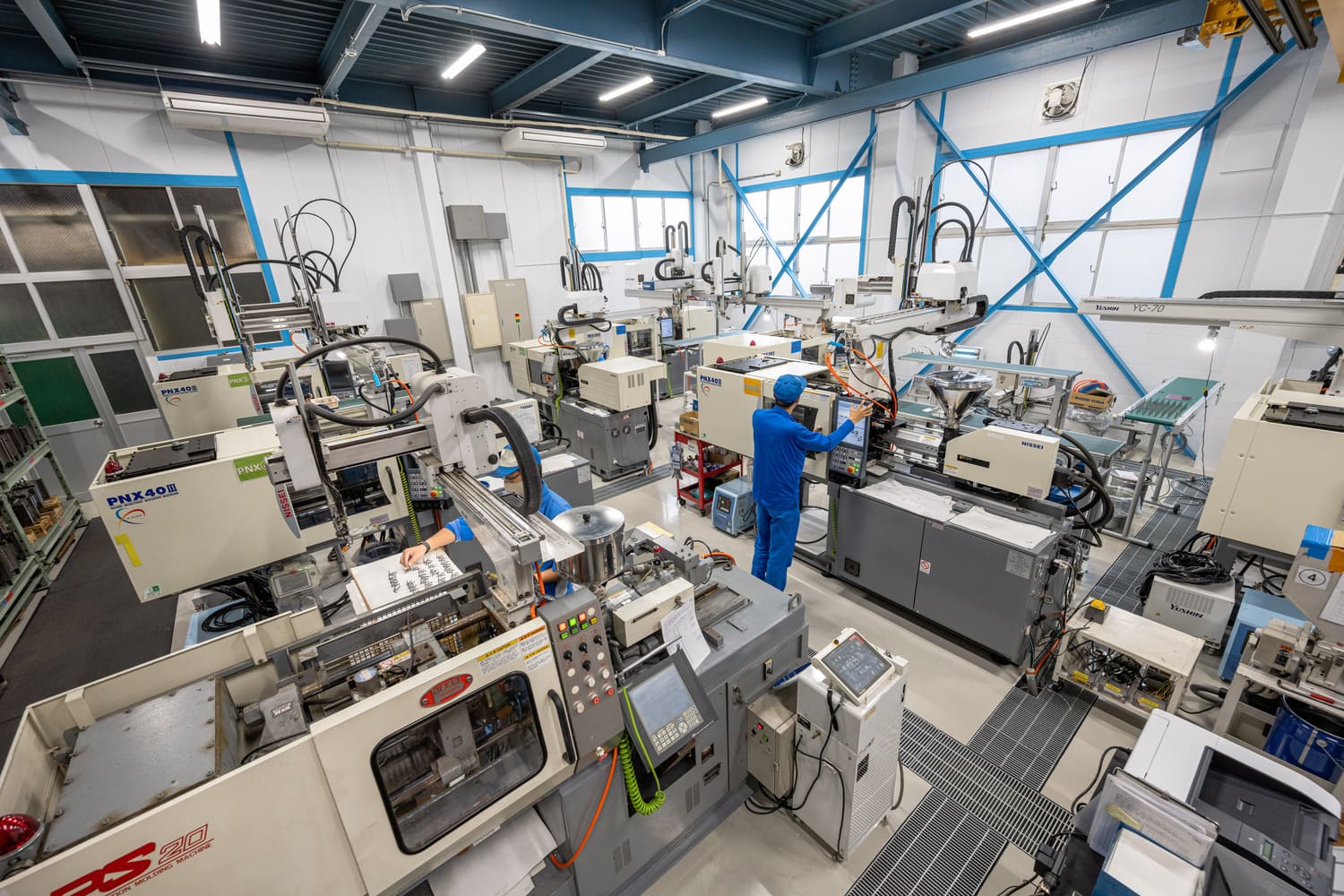
Differences between MIM and μ-MIM®
3D-μMIM® Technology
3D-µMIM® is our unique lost-core process that enables the mass production of components with complex geometries with hollow structures and undercuts that are difficult to fabricate using conventional MIM or machining. First, a plastic mould is produced and placed in the mould to be inserted; the SP mould is completely disassembled in a process of debinding and sintering and finally becomes a 100% metal component.

Sacrificial plastic mould
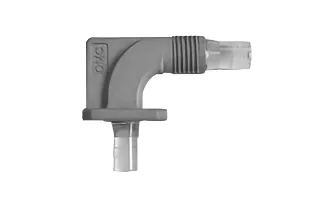
Metal feedstock injection
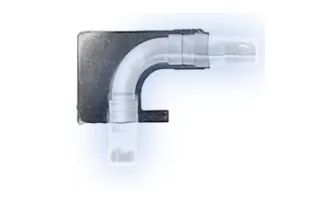
Degreasing and sintering
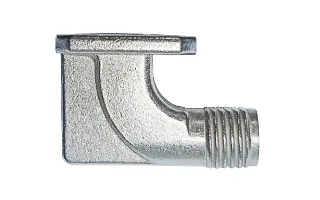
Sintered component
Free-form component examples with 3D-μMIM®
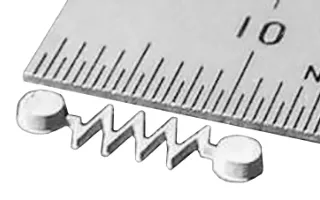
Zigzag spring
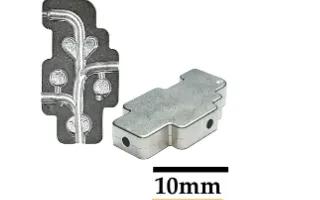
Inner curved flow
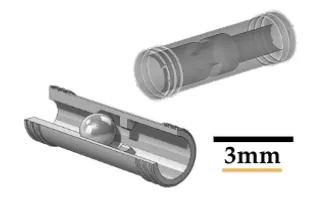
Hollow structure
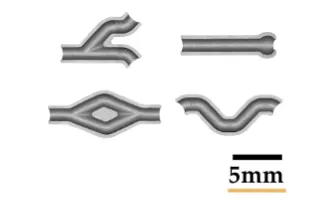
Micro pipe
Schedule a free initial consultation with one of our experts
We will gladly answer your open questions and show you how we can help you solve your technical challenges.