Device
LMM 3D printer: Hammer Lab35
The LMM (Lithography-based Metal Manufacturing) process is characterized by shaping through photopolymerization of a mixture of photosensitive resin and metal powder. Due to the light, lamination is extremely stable and can realize high-precision and small components.
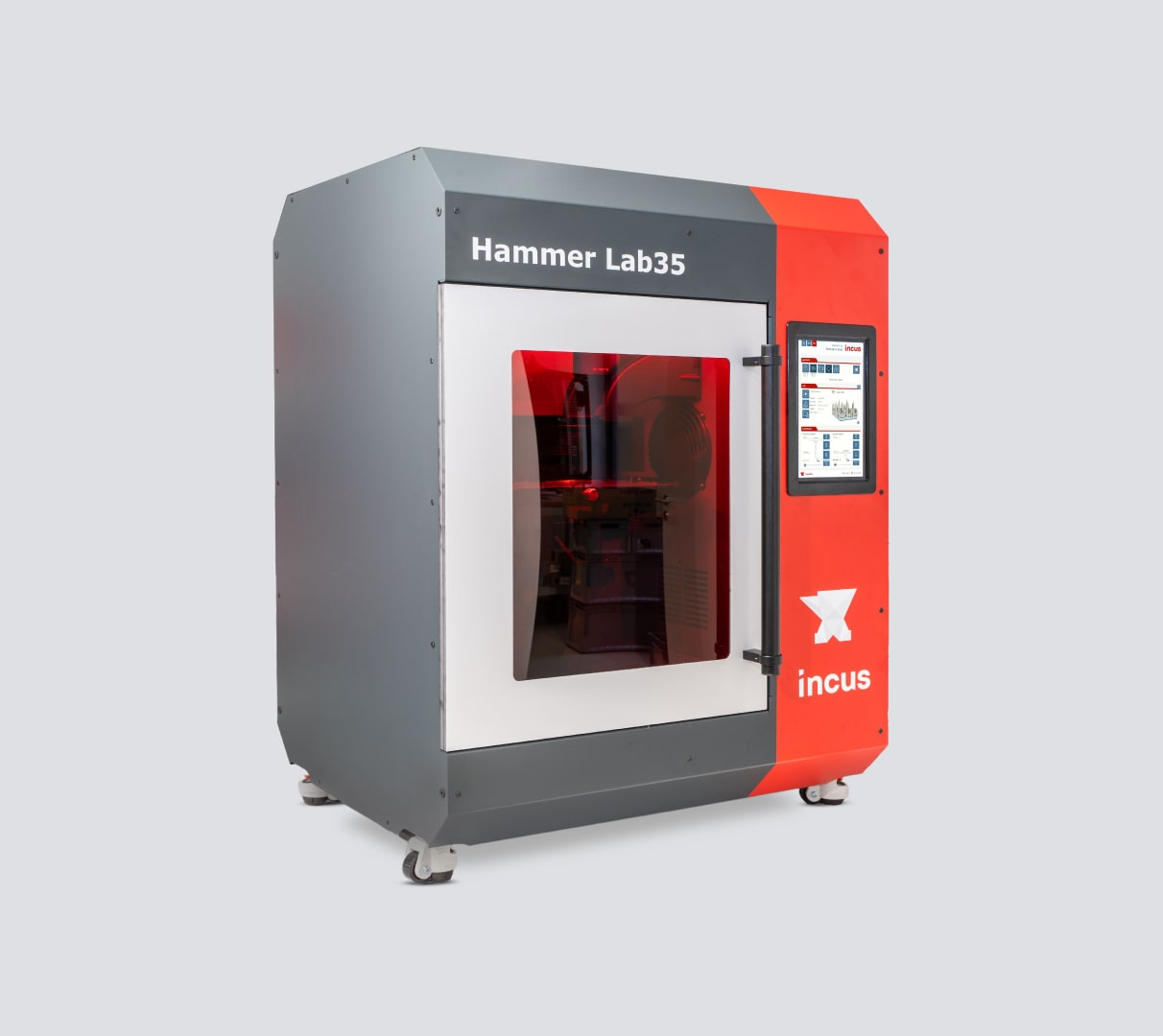
Machine Parameters for Hammer Lab35
Made by
Incus GmbH
Lateral resolution
35 / 15 μm (customised)
Number of pixels (X, Y)
2560x1600
Building Volume (X, Y, Z)
89,6 x 56 x 120 mm
Slice thickness
10 - 100 μm
Building chamber
Full climate control
Building velocity
Up to 250 slices/h
Print speed
Up to 100 cm3/h
3D printing process
This method uses light to form a green body from a mixture of photosensitive resin and metal powder through photo-polymerisation and then dewaxing and sintering to produce a metal modelling product, which is the same as the MIM method after dewaxing and sintering. The advantage is that the material and sintering technologies of μ-MIM® can be deployed as they are. As light is used, stacking is extremely stable and component accuracy of ±0.2% or less is possible. In addition, the workpiece can be removed after moulding without any force being applied to it, making it possible to mould delicate and complex shapes. As a result, quality comparable to μ-MIM® can be achieved.
Advantages of LMM
Print complex-shaped components
It is possible to print microscopic and complex shaped parts with a quality close to that of μ-MIM®.
Use the same equipment and technology
The same equipment and technologies used in μ-MIM® technology can also be used in this process.
Achieve very high precision for components
Tolerances of less than 0.2% are possible with this method.
Collaboration between 3D Printing and μ-MIM®
One of the barriers to the use of μ-MIM® in the past was the lead time and cost during prototyping and small lot production. Now, with the addition of metal 3D printing equivalent to μ-MIM® as an option for our customers, we can support you right from the prototype and small lot production stage - not only with MIM technology, but also as a partner for micro and complex shaped metal components.
Take a look at some components manufactured with 3D printing
Material
Size
Gear
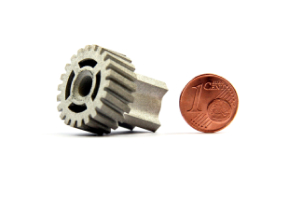
Stainless Steel
φ15mm
Nozzle
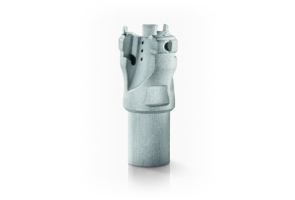
Titanium Alloy
φ10×30mm
Schedule a free initial consultation with one of our experts
We will gladly answer your open questions and show you how we can help you solve your technical challenges.