μ-MIM® Technical Newsletter Vol. 18: TAISEI KOGYO and MICRO MIM JAPAN
In this issue, we will introduce our history and relationship of TEISEI KOGYO CO., LTD. and Micro MIM Japan Holding Inc.
The beginning of metal injection moulding or MIM production at TAISEI KOGYO
TAISEI KOGYO was established in January 1972 with the plastic injection moulding as our main business. We grew rapidly during the high economic growth period in the 70s/80s. While developing the plastic injection moulding technology at our head quarter, our metal powder injection moulding research lab was established at Kyoto Research Park in 1994. Metal injection moulding or MIM material, so-called feedstock is a mixture of metal powder with resin and performs injection moulding to give a desired shape. We considered the binder (resin) is the key to success in metal injection moulding or MIM process, thus, from the early stage of our metal injection moulding or MIM research we have focused on our original binder development.
Establishment of µ-MIM technology
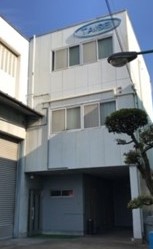
We mass-produce small complex designed metal injection moulding or MIM components, which are impossible for competitive MIM manufacturers, applying our unique knowledge and achievements such as developing our original binders . In particular, the manufacture of micro metal injection moulding or MIM parts, we have acquired a registered trademark in Japan as μ-MIM® (Micro MIM) technology. This µ-MIM® technology is bolstered by our original binders, which packed with original technologies accumulated since the foundation.
TAISEI KOGYO and Micro MIM Japan
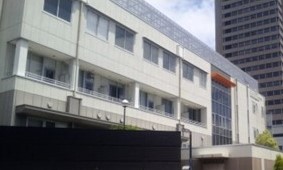
In December 2017, we established Micro MIM Japan Holdings Inc. as a mother company of TAISEI KOGYO CO., LTD. and TAISEI KOGYO (THAILAND) CO., LTD. Micro MIM Japan provides MIM and other high quality Japanese manufacturing technical consulting services, manufacturing development supports, and evaluation (analysis and measurement) services. Additionally, in this year we will evolve our R&D lab at Creation Core Higashi Osaka (since 2010) and our sales representative offices in Offenburg in Germany (since 2016).
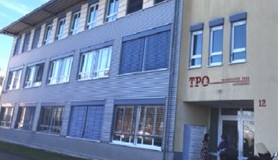
Introduction of TAISEI KOGYO THAILAND
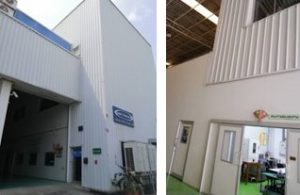
TAISEI KOGYO (THAILAND) CO., LTD. was established in August 2011. There was a serious flooding in 2012 in Thailand. At that time, we were starting up the factory, and fortunately, the sintering furnace just arrived at the port when the flooding occurred near our factory, so our furnace did not suffer any damage before the operation.
We have about 20 employees and most of them are working as inspection staff. Fortunately, our staffs are dexterous and the appearance of minute components is inspected one by one using tweezer. The sintering furnace employed in Thailand factory is with the highest production efficiency in our company. The production capacity is not full yet, thus we look forward to your new inquiries.
Column
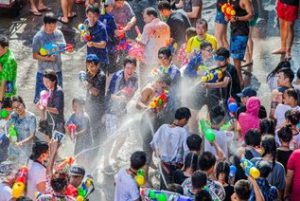
Songkran Festival is Thai New Year’s national holiday in Thailand (13th -15 th April) every year. This festival is very important for Thais to show respect to the parents and relatives. Most of Thais will return to their hometown to see their beloved people and celebrate “water festival” in their hometown. “Water festival“ or “water splash fights” are held all over the country. This period brings joy and happiness to all Thais every single year. Why not visit Thailand during this festival period and enjoy the festival with the Thais?
Conclusion
Cracking, slumping or blistering is commonly observed due to the binder swelling and/or residual stress difference between the surface and interior. It is possible to avoid these problems by selecting appropriate organic solvents and temperature control.
The catalytic deboning uses sublimation of binder, thus it is possible to decompose the binder in relatively short processing time with minimizing the deformation. However, with a strong acidic atmosphere, theapplicable metal material option is limited.
In the sintering process, the necking, which is bridging the metal powders by thermal diffusion, starts at the sintering temperature. Once the necking starts, the shrinking is observed and increases the density, thus before starting the necking reaction, all the organic components should be decomposed and gas between the powders should be removed. In the sintering process, the unwanted chemical reaction, such as oxidation or carbonization, leads to mechanical property loss, therefore a precise atmosphere control with low heating rate at the beginning of the process is required. Also, when it reaches the sintering temperature, some add it vegetal can be evaporated.