μ-MIM® Technical Newsletter Vol. 38: μ-MIM Measurement Technology
μ-MIM technology is characterised by its ability to mass produce less than 100 μm thin structure, 3D complex structure (curved and undercut hollow, free-form surface), and sharp edge structure with high precision in net-shape forming. Here are several applications that take full advantage of μ-MIM technology below.
(1) Micro forcep
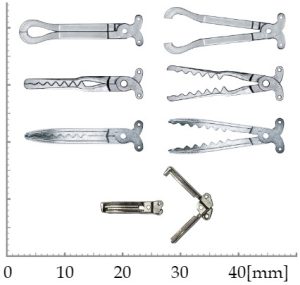
Since the metal components for medical use that require 3D positional accuracy, thus the number of inquiries are increasing. The left picture is examples of forceps with a 20 mm or shorter length design, called micro forceps. A great positional stability of the forceps is also certified, since secondary machining is reduced to zero or minimum. Under our ISO13485-certified quality management system, we guarantee the quality of complex-shaped components by conducting non-destructive measurements.
(2) Micro gear
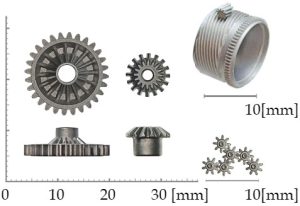
Using our technology cultivated through years of experience in precision MIM, we stably mass produce various types of gears such as bevel, miter, helical and others with 3 mm or less diameter, modulus of 0.025 mm, multi-step or shaft integrated gears. In particular, the integrated helical and spur gears and the corresponding helical gears shown on the left picture are examples that clearly demonstrate the characteristics of μ-MIM technology. We mass-produce complex and small gears with good positional stability. Our quality evaluation technology of micro gears is also receiving high customer satisfaction.
(3) Sharp edge
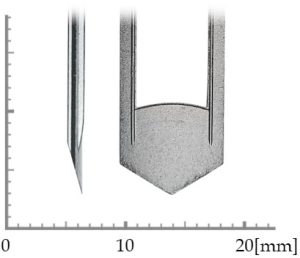
This is an example of 10 μm sharp edge structure with 5 μm radius. Since μ-MIM binders are developed for stable production of small and complex components, which are difficult to mould with conventional MIM. We mass produce knives, blades, and other parts that require sharp edges without post-polishing.
Conclusion
The above are just a few applications that we can disclose to the public. μ-MIM technology realises mass-production with stable quality. As a company, we look forward to your inquiries that are difficult to mass-produce by machining or given up producing by conventional MIM.
Exhibition
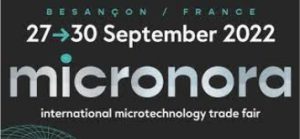
From 27 to 30 September 2022, we will have a stand at the Micronora trade fair in Besançon, France, which is the largest micro technology exhibition in Europe. We would be delighted to welcome you to our stand to see and touch our actual μ-MIM parts.
Column
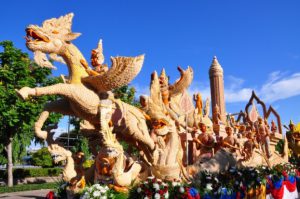
Since we have a blanch in Thailand, fab and R&D, there is a special buddhist holiday in July, Lent day, so let us introduce the event. From this day on, monks are confined to the temple for approximately three months to devote themselves to Buddhist practice. Tourists can attend to see people dedicating large candle festival cars to temples on this day.
Conclusion
Cracking, slumping or blistering is commonly observed due to the binder swelling and/or residual stress difference between the surface and interior. It is possible to avoid these problems by selecting appropriate organic solvents and temperature control.
The catalytic deboning uses sublimation of binder, thus it is possible to decompose the binder in relatively short processing time with minimizing the deformation. However, with a strong acidic atmosphere, theapplicable metal material option is limited.
In the sintering process, the necking, which is bridging the metal powders by thermal diffusion, starts at the sintering temperature. Once the necking starts, the shrinking is observed and increases the density, thus before starting the necking reaction, all the organic components should be decomposed and gas between the powders should be removed. In the sintering process, the unwanted chemical reaction, such as oxidation or carbonization, leads to mechanical property loss, therefore a precise atmosphere control with low heating rate at the beginning of the process is required. Also, when it reaches the sintering temperature, some add it vegetal can be evaporated.