μ-MIM® Technical Newsletter Vol. 21: Materials with high hardness
We receive more inquiries about special gears and small metal parts for medical precision machines by materials with high hardness. Today we will introduce our experienced materials which are harder than stainless steel 316L, commonly employed in metal injection moulding or MIM production.
Powder material for MIM
The metal powder is generally more expensive than in other forms such as rod or plate, and additionally, the metal powder for metal injection moulding is expensive even among whole powder metal material. There is a certain price difference between stainless steel and carbon steel in plate or rod material. However, in MIM powder there is no price difference between stainless steel and carbon steel because its processing cost dominates the price. Therefore, stainless steel powder is commonly deployed in the metal injection moulding (MIM) industry since it is possible to eliminate the plating or other post-treatments to improve the corrosion resistance.
Today, it is increasing the demands of high hardness aside from the corrosion resistance, not only for special gears but also for small metal parts for medical devices. The less invasive medical treatment are studied and developed intensively, and it is required smaller and more complicated metal parts to realise the treatment. The smaller the part, the higher the stress it receives during the treatment, thus it requires good mechanical properties with high hardness in the components. Furthermore, it is possible to consider that the simulation techniques have been developed so that the stress and heat energy are calculated accurately for precise prediction in the parts development phase.
It is well known that the carbon steel has high hardness, and we have experienced serial production of AISI4140, which is equivalent to SCM440. The hardness achieved is 700-1000Hv with the heat treatment, however, the corrosion resistance is very low thus it is required to store with an anti-rust agent. In small and complicated designed metal components, it is difficult to remove the anti-rust agent or to give uniform plating. If it is possible to produce these components by high hardness with good corrosion resistance, those problems will be solved.
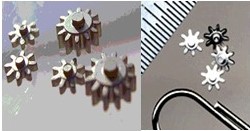
Material with high hardness for μ-MIM®
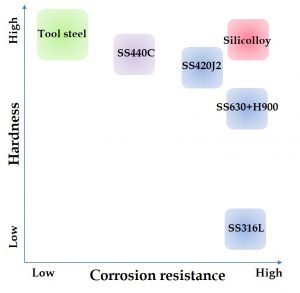
We introduce high hardness materials with good corrosion resistance from our experience. Stainless steel 17-4PH (SS630) has higher hardness than austenitic type stainless steel, e.g. SS316L, with the appropriate heat treatment. 17-4PH is classified as precipitation hardening stainless steel because its hardness is increased by precipitation of copper. The other precipitation hardening stainless steel is Silicolloy*, which is hardened by silicon precipitation, possesses higher hardness than 17-4PH. Stainless steel 420J2 also has high hardness. It is a martensitic type stainless and its hardness is increased by heat treatment. We have experienced productions of not only stainless steels but also titanium, titanium alloy, tungsten alloy and so on. Please contact us if you are seeking a precise serial production of small, complicated components with high hardness.
Column
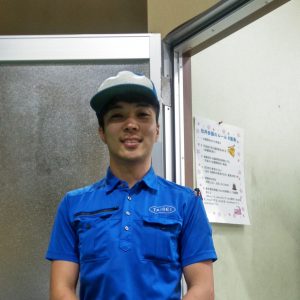
Hello. I am Yuta Miyazaki, in charge of the appearance inspection and material-feedstock assessment in the injection moulding process. I have realised how important the control of the material or feedstock quality in MIM production is since the injected part appearance reflects the feedstock quality. I love to spend my time taking care of my car. It takes about 2 hours every weekend to clean my car up until its body shines so that it keeps its cleanliness for a week. Recently, I visited a Turkish restaurant, run by a Turkish person and I was very impressed with my first bite on the Turkish dish there. Since then, I got more interested in international cuisine.
Conclusion
Cracking, slumping or blistering is commonly observed due to the binder swelling and/or residual stress difference between the surface and interior. It is possible to avoid these problems by selecting appropriate organic solvents and temperature control.
The catalytic deboning uses sublimation of binder, thus it is possible to decompose the binder in relatively short processing time with minimizing the deformation. However, with a strong acidic atmosphere, theapplicable metal material option is limited.
In the sintering process, the necking, which is bridging the metal powders by thermal diffusion, starts at the sintering temperature. Once the necking starts, the shrinking is observed and increases the density, thus before starting the necking reaction, all the organic components should be decomposed and gas between the powders should be removed. In the sintering process, the unwanted chemical reaction, such as oxidation or carbonization, leads to mechanical property loss, therefore a precise atmosphere control with low heating rate at the beginning of the process is required. Also, when it reaches the sintering temperature, some add it vegetal can be evaporated.