μ-MIM® Technical Newsletter Vol. 22: Mass production technology of metal components with thin wall
This SEM image shows a part of a thin-wall component we mass-produced, and its edge thickness is only 10 μm. It is required not only the mould and processing technique but also adequate material development.
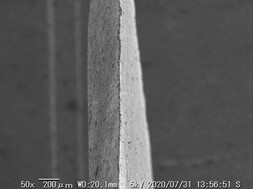
In mould design for thin-wall structure components, it is well known that it is important to consider the gas extract upon injecting the feedstock (FS). Especially with the thin-wall structure moulding, the injection speed will be relatively fast since the FS temperature drops fast. Therefore the gas extract during the injection is significantly affected by the quality of thin-wall green parts. Furthermore, in mould tooling, fine polishing skill is required which realises the perfect parting line contact since the ultra-fine powder is deployed normally in our thin-wall component production. The smaller and thinner designed components, the shorter the injection time is, therefore, high flowability FS is deployed. Generally, high flowability FS are brittle and the thin-wall design is difficult to demould. Our μ-MIM® technology has developed the FS for thin-wall structure mass production. Please also have a look at our newsletter Vol. 12 about our binder details. click
Exhibition
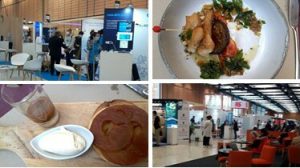
We participated in the trade fair “SIDO” on 3rd – 4th Sep. in Lyon, France for the first time after the COVID lockdown. About 350 companies exhibited and there were almost 8500 visitors in total (about 1700 visitors were online/7800 visitors in real).
This exhibition was for robot industries. It is said that the world market of AI and service robots (excluded the production processing robots) would grow to 263.4 million€ in 2026. We have experienced mass production of metal components for robots and wearable products so we had fruitful discussions there.
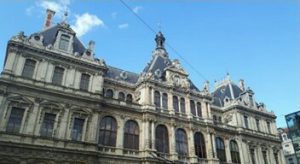
Lyon is famous as a city of gourmet and an international food industry exhibition “SIRHA” is held every 2 years. Furthermore, the museum “La Cité International de la Gastronomie” opened in 2018, which shows food culture, health and life quality related to food, French lifestyle and so on. Besides the business discussions, we enjoyed the delicious cuisine.
Column
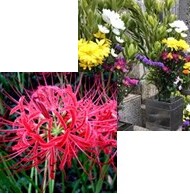
In the mid September, Japan has a traditional period called „Higan“ for a week. During Higan, we visit family‘s graves and greet our ancestors with flowers and offering. It is believed that this behaviour must lead us to the paradise after our dead. Lycoris radiata blooms as if it would announce this Higan-period. This is a reason why it is called „flower of Higan (Higanbana)“ in Japan. Other flowers such as Chrysanthemum and lily are decorated at the graves, therefore cemetaries seem a kind of flower gardens.
Conclusion
Cracking, slumping or blistering is commonly observed due to the binder swelling and/or residual stress difference between the surface and interior. It is possible to avoid these problems by selecting appropriate organic solvents and temperature control.
The catalytic deboning uses sublimation of binder, thus it is possible to decompose the binder in relatively short processing time with minimizing the deformation. However, with a strong acidic atmosphere, theapplicable metal material option is limited.
In the sintering process, the necking, which is bridging the metal powders by thermal diffusion, starts at the sintering temperature. Once the necking starts, the shrinking is observed and increases the density, thus before starting the necking reaction, all the organic components should be decomposed and gas between the powders should be removed. In the sintering process, the unwanted chemical reaction, such as oxidation or carbonization, leads to mechanical property loss, therefore a precise atmosphere control with low heating rate at the beginning of the process is required. Also, when it reaches the sintering temperature, some add it vegetal can be evaporated.