μ-MIM® Technical Newsletter Vol. 29: Fronteering the SDGs Binder
Our binder system developed by μ-MIM® technology realised 100% material yield, yet we keep seeking a new binder that realises more SDGs in MIM production. This time we will introduce some potential binder system for future use.
Targeting binder type
We use a mixture of plastic polymer and wax, called binder for MIM feedstock. Our original feedstock will be injection moulded in small and complicated green parts and the binder will be fully decomposed during the debinding and sintering process. Thus, our original binder works very hard in a very short time behind the production scenes. The binder in MIM production is required to have a high affinity to the functional moiety on the metal powder surface, thus polarised polymer is applicable. Our binder contains polyoxymethylene (POM) which is a polarised polymer. Here let us show a closer polarised polymer candidate to achieve SDGs.
Candidates
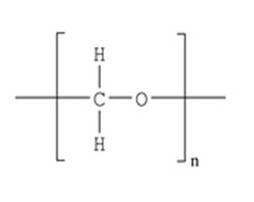
1. Polylactic resin
It is well known as a biodegradable polymer for a long time. Polylactic resin is made from sweet cones and some of the manufacturers are successfully commercially producing. The ester moiety can be working as a functional moiety in the binder system.
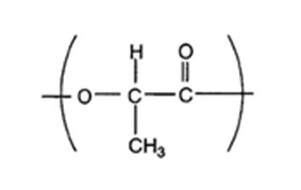
2. Agarose
The natural polymer, agar, can be a candidate since it is composed of polysaccharide and the water-soluble function draws renewed attention from MIM industry. Some MIM component manufacturers already deploy agarose base binder in their serial production. Up until now, we were not successful yet. However, another natural polymer from seaweed, algin acid can be our binder candidate.
We will keep seeking the new binder to achieve a higher level of SGDs through our μ-MIM® production.

Column
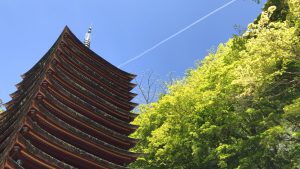
In Japan, we enjoy the new greens (Shinryoku in Japanese) on the trees in spring to early summer (between March to June). The word Shinryoku is a word used in Haiku (Japanese traditional poem) to express the season.
In this photo, you can see a beautiful contrast of the young green against the blue sky and the pagoda of a temple.
We hope you are enjoying the summer time and come to visit us in Japan when the pandemic is over.
Conclusion
Cracking, slumping or blistering is commonly observed due to the binder swelling and/or residual stress difference between the surface and interior. It is possible to avoid these problems by selecting appropriate organic solvents and temperature control.
The catalytic deboning uses sublimation of binder, thus it is possible to decompose the binder in relatively short processing time with minimizing the deformation. However, with a strong acidic atmosphere, theapplicable metal material option is limited.
In the sintering process, the necking, which is bridging the metal powders by thermal diffusion, starts at the sintering temperature. Once the necking starts, the shrinking is observed and increases the density, thus before starting the necking reaction, all the organic components should be decomposed and gas between the powders should be removed. In the sintering process, the unwanted chemical reaction, such as oxidation or carbonization, leads to mechanical property loss, therefore a precise atmosphere control with low heating rate at the beginning of the process is required. Also, when it reaches the sintering temperature, some add it vegetal can be evaporated.