μ-MIM® Technical Newsletter Vol. 20: Manufacturing Part 2 – collaboration of metal AM and metal injection moulding (MIM)
Today we subsequently introduce our approach to collaborate with AM and our prospects.
Summary of metal AM
These days, various metal AM devices have been developed and they are in fierce competition to survive in the market. There are strengths and weaknesses derived from their manufacturing processes as summarised in the following table.
The table classifies representative AM methods by the densify phase.
Comparison table of representative metal AM methods
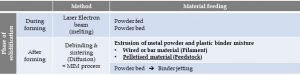
Coexistent of MIM with AM
The process, densifying step comes after the forming, requires debinding and sintering steps which are same and essential as in metal injection moulding or MIM process. Therefore, we could apply our metal injection moulding processing technology to some metal AM processing. With the fused deposition modelling (FDM) method, shown as bold letters in the table, it is commonly employed wire or bar form filament to form the green body. Recently, a metal AM device* has introduced in the market which employs pelletised MIM-feedstock directly. Therefore, it is allowed to say that the FDM method is the best way for MIM manufacturer to collaborate with AM manufacturing. Since we have knowledge and experience with our feedstock over our metal injection moulding production history, both our techniques of debinding and sintering step and of forming step should be effective also in metal AM devices. We believe this collaboration will lead our better service for customers, especially for the prototype production phase.
Our approach to the AM manufacture
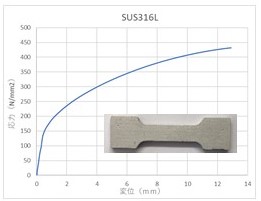
We have studies with our original feedstock applied in FDM metal AM device and it is observed the mechanical properties. The graph shown in right is a result of a tensile test. We confidently offer our feedstock for AM trial to whom has problems with metal AM manufacturing. Please do not hesitate to contact us.
Column
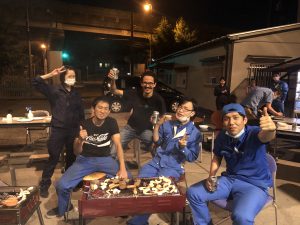
At Micro MIM Japan Holdings Inc. & Taisei Kogyo Co., Ltd. headquarters in Osaka, Japan, we have a BBQ evening twice a year. This is organised by some of the young colleagues who work at the HQ. The event starts at 6.00 PM when everyone finishes the work. Last time we brought a PC out and connected with the colleagues in Thailand and Germany. This was a good opportunity for everyone to say hi to each other and see how the colleagues in other locations are doing. Especially after the lockdown, people were happy to see each other even online. The downside of those who are not in Japan was that while the colleagues in Japan were enjoying beers and BBQ, we had to work!
Conclusion
Cracking, slumping or blistering is commonly observed due to the binder swelling and/or residual stress difference between the surface and interior. It is possible to avoid these problems by selecting appropriate organic solvents and temperature control.
The catalytic deboning uses sublimation of binder, thus it is possible to decompose the binder in relatively short processing time with minimizing the deformation. However, with a strong acidic atmosphere, theapplicable metal material option is limited.
In the sintering process, the necking, which is bridging the metal powders by thermal diffusion, starts at the sintering temperature. Once the necking starts, the shrinking is observed and increases the density, thus before starting the necking reaction, all the organic components should be decomposed and gas between the powders should be removed. In the sintering process, the unwanted chemical reaction, such as oxidation or carbonization, leads to mechanical property loss, therefore a precise atmosphere control with low heating rate at the beginning of the process is required. Also, when it reaches the sintering temperature, some add it vegetal can be evaporated.